3D printing, also known as additive manufacturing, is becoming more and more common in turbocharger development. Based on a CAD (computer-aided design) model, the 3D printer can create a three-dimensional object, such as a turbocharger component. This is very useful in the early development phase of a new turbocharger.
3D printing of prototypes is a lot faster than the traditional method of rapid mold casting. By using 3D printing, several weeks can be saved per prototype, thereby saving time and costs. Additionally, 3D printing offers more freedom in design. It’s a completely different manufacturing process, which provides new opportunities in turbocharger design.
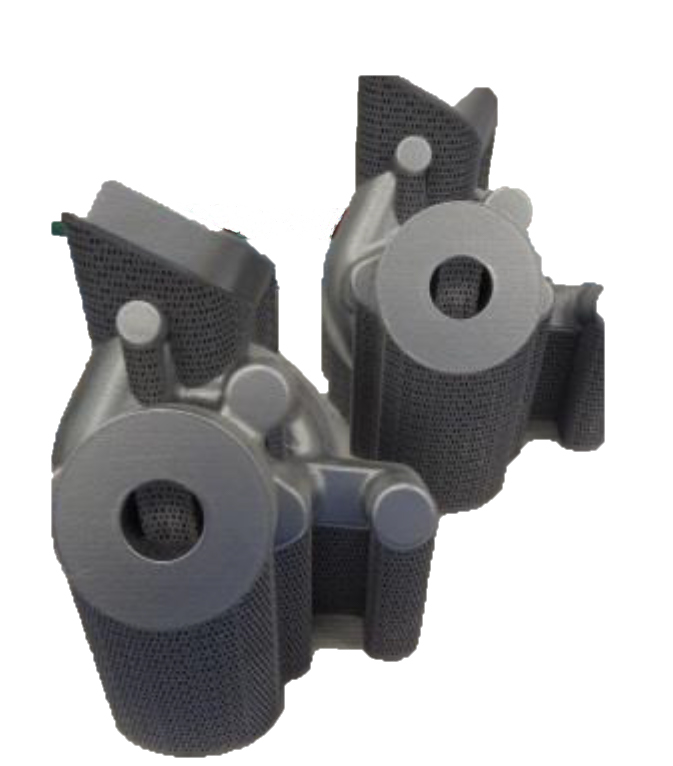
Finished 3D printed parts
3D printing has also become popular in many other industries where high-precision products are made such as aerospace, medical, railway etc. The only shortcoming of 3D printing is the cost. Therefore, it is only possible to use it for complex models of which you only need a few.
However, costs are projected to keep declining in the coming years opening up to more opportunities. It is even expected that 3D printing will be used to print spare parts on location in the future, for some industries, saving inventory, time and delivery costs. A few companies are already experimenting with this.
It seems clear that we haven’t seen the full potential of 3D printing yet. It will be interesting to see how it can add further to turbocharger development and manufacturing in the future, as well as to other industries.