Optimizing the heart of the turbocharger
In the competitive automotive market, the performance of turbochargers is constantly being pushed towards their theoretical optimum.
So begins the thesis of Rob Eling who obtained his PhD in May of this year. Rob undertook five years of research into cartridge design optimization, which led to great results that could be put into practice.
The cartridge is often referred to as the heart of the turbocharger as it determines the performance of the entire device. The design of the cartridge affects overall turbocharger efficiency, reliability, friction losses, noise output and costs.
The cartridge often runs at speeds above 200,000 rpm. At these extreme speeds, manufacturing variations within a fraction of a hair have a huge impact on performance. So with these high speeds, you need to have everything in control; Rob explains.
Rob had already been working for several years at MTEE when he realized the great potential of optimizing the cartridge design of our turbochargers. As a former graduate from Delft University of Technology, a close partner university to MTEE, this provided an opportunity for co-operation on this topic. Technische Universiteit München was also part of the partnership.
Delft is one of the top 10 technical universities in Europe and known for its research in dynamics and tribology, so this was an excellent opportunity.
As the task was very challenging and time-consuming, Rob received the help of many students to dig into several fundamental topics. In total, Rob supervised six master students and a bachelor student, all of whom were awarded with excellent grades from the university for their contributions. Furthermore, as it was in the interest of everyone at MTEE to make this study a success, many departments within the organization provided support in the research by creating test set ups and developing prototypes and so forth. Rob analyzed the complete cartridge system including the bearings, rotor and bearing housing, and was able to optimize the geometry while keeping in mind the sensitivity of the design to typical dimensional variations encountered in series production. A complex multi-physical model was built which took the Delft’s supercomputers many hours to run. To see if the predictions were correct, measurements on a test set up were performed. With the validated model, Rob was able to analyze the critical areas of optimization. This not only improved the performance of the cartridge, but also made it more cost-efficient due to a design that required a less expensive production process.
Making one good turbocharger is relatively simple. But if you want to make thousands of turbochargers at a competitive price, a cost-efficient design is critical. You need to know exactly which tolerances must be tight and which tolerances are less sensitive to variation.
Rob started his career at MTEE 10 years ago as a student doing his master thesis on the topic of the dynamic behaviour of turbocharger bearing systems. Back then his research focused on understanding the behaviour of the rotor-bearing system. With his PhD, Rob moved on to researching how to improve it. In the meantime, an official R&D department was set up at MTEE – the first and only one outside of Japan. Today, Rob is part of the R&D team and is responsible for developing electric boosting systems.
For those who are interested, Rob’s PhD thesis can be found here:
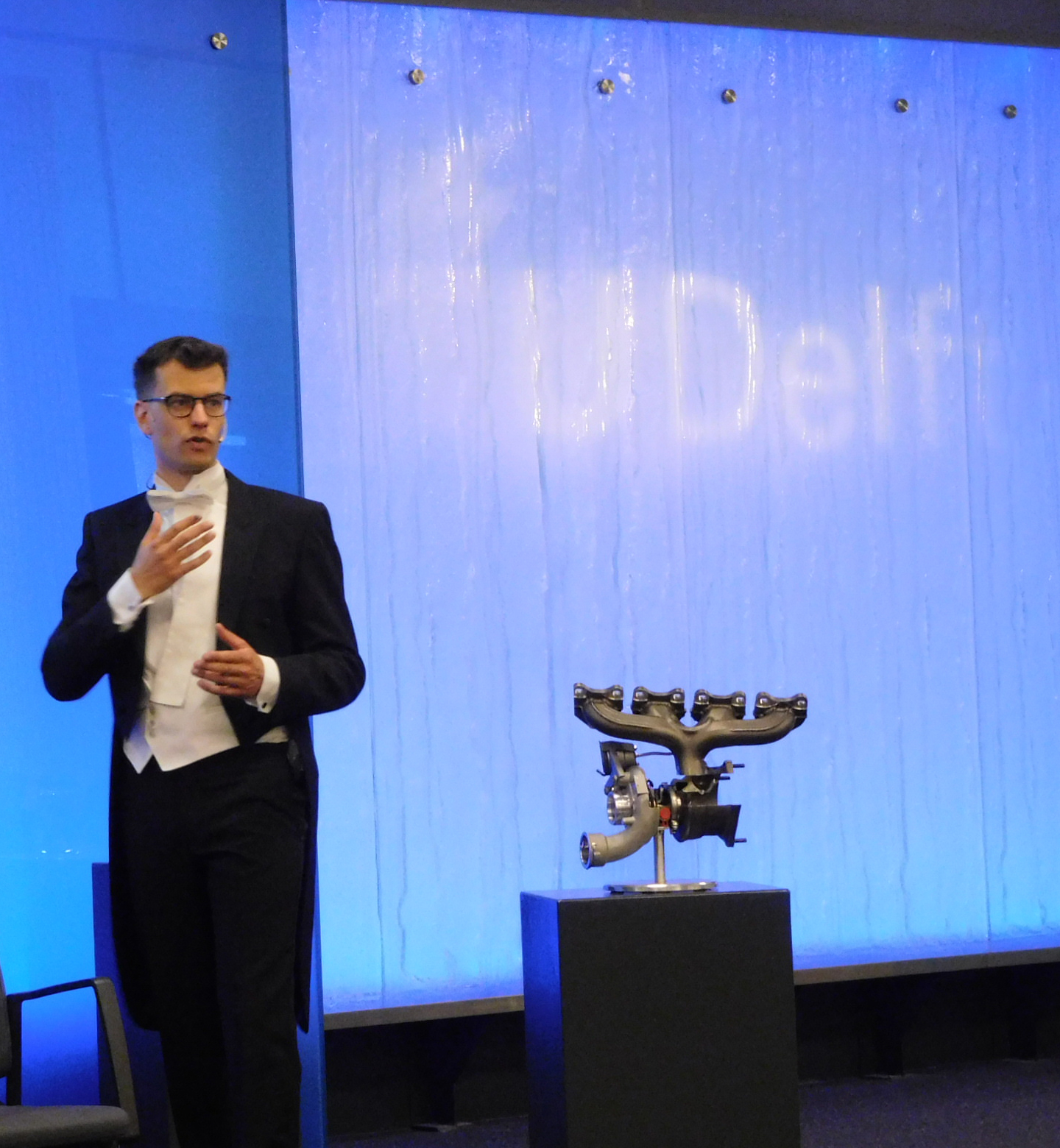